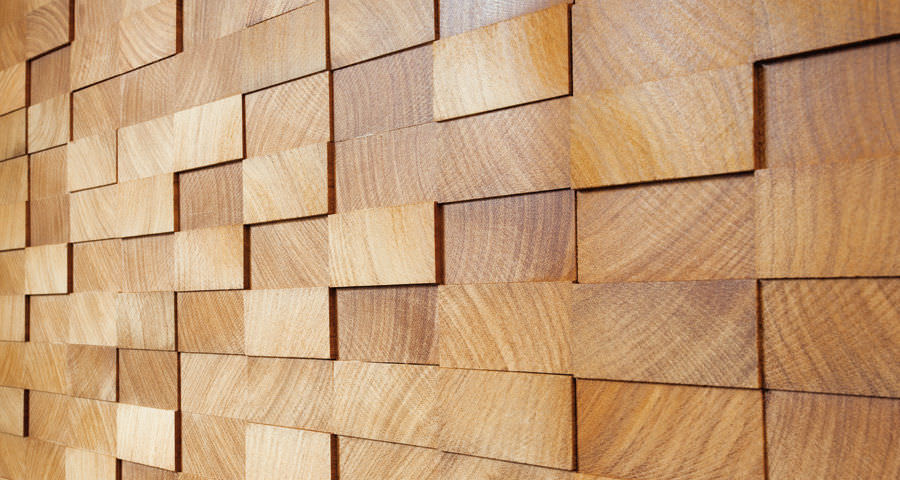
PANNELLI
Attraverso le tecniche di sfogliatura e tranciatura si ottengono fogli di legno sottili che, opportunamente assemblati, danno vita a diverse tipologie di pannelli: compensati, paniforti, pannelli sandwich e tamburati sono il risultato delle diverse modalità di unione dei fogli di legno, inoltre la necessità di risparmiare e di utilizzare ogni parte del tronco dà vita ai pannelli di particelle, di fibre e di lana di legno costituiti da frammenti di diverse dimensioni assemblati con l’uso di colle.
Questi prodotti offrono alcuni evidenti vantaggi rispetto alle Tavole di legno massello. Innanzitutto la possibilità di ottenere pannelli di notevoli dimensioni e di spessore molto diversificato (compensati, più sottili, e pannelli sandwich, più spessi), oltre che più leggeri e più resistenti (in particolare i tamburati). Inoltre i derivati presentano caratteristiche di resistenza uniformi, non più condizionate dalla direzione delle venature. A questo va aggiunta una maggiore stabilità dimensionale determinata dall’assemblaggio dei fogli che segue una logica di incrocio delle venature, dunque essi presentano una minore sensibilità alle variazioni dell’umidità atmosferica. Infine, alcuni pannelli offrono un’alta capacità coibente (in particolare quelli a base di lana di legno e quelli a base di fibra di legno).
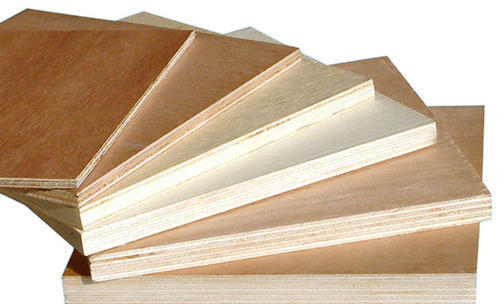
Le principali controindicazioni relative ai derivati del legno riguardano la presenza, pressoché inevitabile al loro interno, di collanti di diversa natura e, con rare eccezioni, di tossicità accertata.
– Pannelli stratificati
1. Compensati:
il termine deriva dalla possibilità di compensare le deformazioni naturali del legno attraverso l’incollaggio a pressione di fogli di tranciato o sfogliato, paniforti, tramezzini e tamburati: particolari tipi di compensati, i paniforti sono composti da un’anima in listelli o lamelle di legno massello (pioppo, abete, o pino) rivestita sulle due facce da fogli di tranciato o sfogliato di spessore compreso tra i 10 e i 30 mm, generalmente di pioppo o betulla, disposti con venatura ortogonale rispetto ai listelli; gli spessori complessivi variano da 10 fino a 50 mm; i tramezzi o pannelli sandwich sono prodotti simili ma hanno un anima in pasta di legno pressata, schiuma di gomma, acetato di cellulosa espanso o fogli di carta ondulata; in tutti casi la parte interna funziona come isolante o pannello di irrigidimento.
Il legno compensato di piallacci presenta un potenziale elevato nella maggior parte dei criteri ecologici considerati (potenziale di riscaldamento globale, acidificazione, PEC e fotosmog). Ciò è dovuto alla quantità di risorse necessarie alla produzione dei piallacci e degli adesivi, all’uso importante di energia elettrica – che a livello europeo (UCPTE-Mix), a causa delle quantità importanti di energia elettrica di origine nucleare o termica, provoca importanti problemi ecologici e si manifesta quindi in modo negativo sul bilancio ecologico -, e ai quantitativi di adesivi utilizzati. La quantità di adesivo nel prodotto è piuttosto importante e quindi anche il suo effetto sulla valutazione globale.
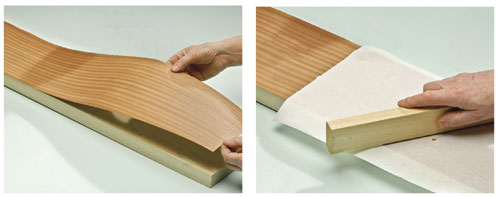
2. Truciolati:
il termine indica l’utilizzo di scarti di legno finemente sminuzzati essiccati, mescolati e incollati a pressione per ottenere pannelli con elevate caratteristiche meccaniche, di basso costo, indeformabili, con minori limiti dimensionali rispetto ai compensati ma di peso unitario maggiore; gli spessori variano da 3 a 24 mm e la lunghezza è determinata in funzione delle necessità, il truciolato infatti è prodotto in nastro continuo tagliato in misure standard. Le facce dei pannelli possono essere lisce e compatte o rivestite con fogli di truciolati e di tranciato o di laminato plastico.
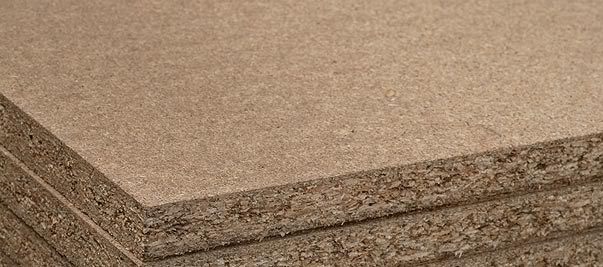
Il limite maggiore dei truciolati è di non poter essere assemblati con tecniche di incastro tradizionali, viti o chiodi; si sono pertanto messe a punto tecniche di assemblaggio che utilizzano elementi complementari come spigoli di massello, spine, biette, profili di plastica o alluminio e metodi di unione con caviglia e bullone; il truciolato inoltre in presenza di umidità eccessiva può gonfiarsi perdendo le sue caratteristiche meccaniche.
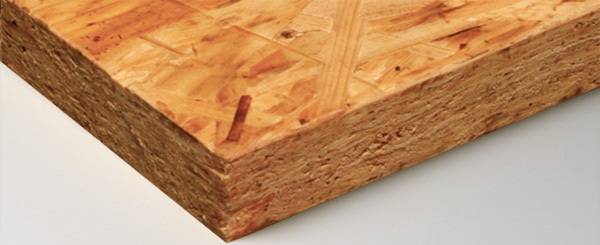
Rispetto alla maggior parte dei criteri ambientali, i pannelli OSB mostrano un potenziale da basso a moderato. Per PEC, risorse abiotiche e potenziale di ossidazione fotochimica, i valori sono tuttavia superiori alla media degli altri materiali a base legno. Ciò è dovuto, nel caso specifico, all’elevato fabbisogno elettrico per la fabbricazione del prodotto, che determina gravi problemi ecologici in tutta Europa (UCPTE-Mix) in virtù dei forti consumi di energia atomica e termica, che hanno un’incidenza negativa sul bilancio, e delle quantità di colla utilizzate. La percentuale di colla nel prodotto è mediamente alta e, pertanto, incide nella stessa misura sull’impatto ambientale complessivo del prodotto.
– Pannelli di fibre:
Prodotti con frammenti e cascami (abete, pioppo o faggio) ammorbiditi al vapore a 170° e opportunamente sfibrati meccanicamente con mole rotanti al fine di ottenere una massa omogenea; da ciò si ottengono diverse tipologie di pannelli utilizzando procedimenti a secco o con addizione di acqua. Si distinguono in teneri meno di 350 kg/m3, semiduri 350-800 kg/m3 o di durezza normale 800 o più kg/m3. I più comuni prendono il nome commerciale di faesite, manosite o MDF. Gli spessori variano da 2 a 11 mm e le dimensioni possono raggiungere i 5 m. Il loro utilizzo nel settore dell’ edilizia varia dalle controsoffittature e rivestimenti in genere alle casseformi.
Rispetto alla maggior parte dei criteri ambientali, il pannello di fibre mostra un potenziale molto basso. Questo è dovuto nel caso specifico al consumo ridotto di energia elettrica per la fabbricazione del prodotto. La percentuale di colla nel prodotto è eccezionalmente bassa e, pertanto, incide nella stessa misura sull’impatto ambientale complessivo del prodotto. Bisogna sottolineare in particolare il fatto che il potenziale di riscaldamento globale del pannello di fibre a bassa densità ha un valore negativo. Infatti, questo pannello mantiene intatto il “credito” per l’immagazzinamento di CO2 che tutti gli altri materiali a base legno compensano invece con l’utilizzo di colla o il consumo elevato di energia per la fabbricazione.
– Pannelli in lana di legno:
Realizzati con striscioline di legno di spessore inferiore al mm, tagliate nel senso della fibratura, impregnate con sostanze ignifughe, antiparassitarie e antiputrescenti, le strisce vengono agglomerate con materiali leganti a formare pannelli rigidi ricchi di cavità irregolari. Lo spessore varia da 1,5 a 7,5 cm e le dimensioni raggiungono i 2 m. Utilizzati solitamente per la realizzazione di controsoffittature e pareti isolanti.
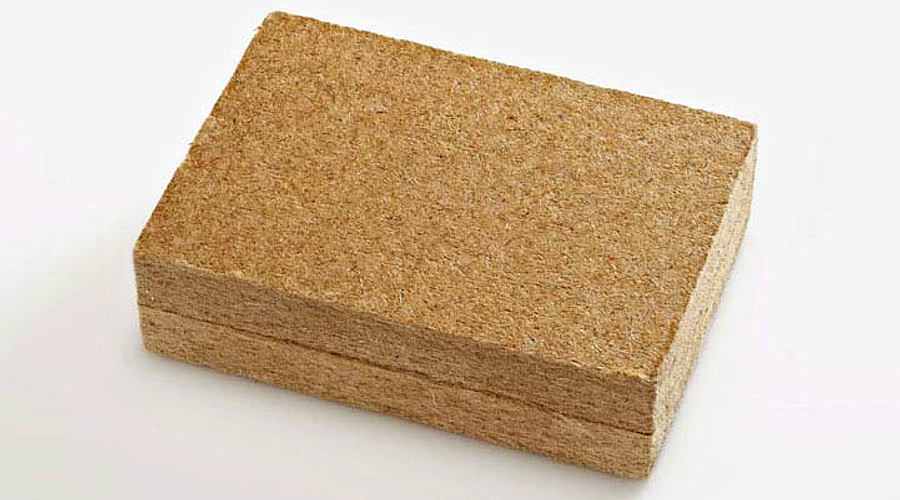